BLDC Motor (Brusless Dynamo) , How a BLDC Dynamo Works and Its Construction. Electric motors are developed in various special types, such as stepper motors, servo motors, permanent magnet motors, etc. Brushless DC motors or BLDC motors are the most suitable for applications requiring high, high efficiency, more torque per weight, etc. This article describes the BLDC motor in detail.
BLDC Motor Construction
The commutator brush arrangement helps in achieving unidirectional torque in ordinary dc motors. Obviously, the commutator and brush arrangement are omitted in brushless dc motors. An integrated inverter/switching circuit is used to achieve unidirectional torque. That is why these motors are sometimes referred to as ‘electronically driven motors’.
Just like other electric motors, BLDC motors also consist of two main parts, namely the stator and rotor. Permanent magnets are attached to the BLDC motor rotor, and the stator is wound for a certain number of poles. Also, the control circuit to the stator winding. Most of the time, the inverter/control circuit or controller is integrated into the stator assembly. This is the basic construction difference between a brushless motor and a regular dc motor.
A typical controller provides a three-phase frequency controlled supply to the stator winding. The supply is controlled by a logistic control circuit and is energized at a specific stator pole at a specific point in time. This can be understood from the animation below on how a BLDC motor works.
Scorpion Brand BLDC Dynamo Design Example
- Aluminum housing with multi-angle cooling holes ensuring through motor while running.
- A threaded prop adapter is included with each motor.
- Differently spaced rear threaded mounting holes to suit various applications.
- Machined aluminum cross style mount with hardware.
- Specially designed NdFeB magnet with high temperature rating for trouble-free operation.
- A durable black Electro-Coat coating on the flux ring to make it look great for years to come.
- High quality stator plates are epoxy coated on the inner surface to prevent shorts from winding. 0.20mm stator plates are used on 22mm motors, with 0.35mm stator plates on the larger sizes.
- High quality shielded ball bearings are used to support the motor shaft in all of our motors.
- 180 C (356 F) High Temperature Wire is used to wind the motor to enjoy the motor burning. The motor is also machined to ensure a consistent roll.
- The high adhesive temperature used to make the stator windings and prevent them from sliding and pinching or shorting.
BLDC Motor Type
There are two types of BLDC motors based on their construction/design:
- Inrunner rotor design: this is a conventional design, where the rotor is located in the core (center) and the stator windings surround it.
- Rotor design (outrunner): In this configuration, the rotor is on the outside. i.e. the stator winding is located in the core while the rotor, carrying permanent magnets, surrounds the stator.
How do BLDC motors work?
BLDC Dynamo stator winding in control circuit (integrated switching circuit or inverter circuit). The control circuit energizes the right windings at the right time, in a pattern that rotates around the stator.
The permanent magnets in the rotor try to align with the energized stator electromagnet, and as soon as they align, the next electromagnet is energized. Thus, the rotor continues to run. The animation below will give you a clear idea of ’how does a brushless DC motor work?’
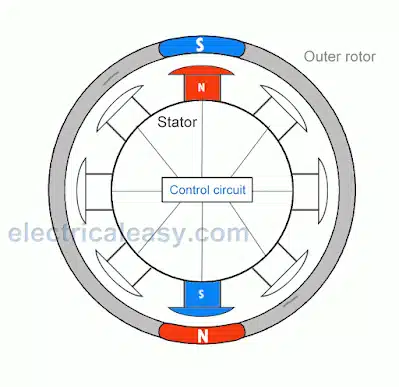
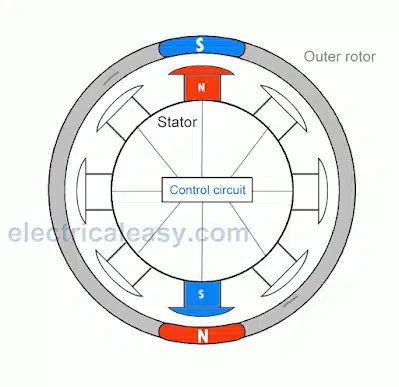
Brushless DC Motor vs. Brushless Use a Brush (Brushed)
- Brushes require frequent replacement due to mechanical wear, therefore, Brushed DC motors require regular maintenance. Also, when the brush transfers current to the commutator, contact occurs. Limits the maximum speed and number of poles the armature can have. All these shortcomings are eliminated in brushless DC motors. An electronic control circuit is required in a brushless DC motor to replace the stator magnets to keep the motor running. This makes the BLDC Dynamo perhaps less rugged.
- The advantages of the improved Dynamo BLDC motor are increased efficiency compared, longer service life, less and less, etc.
BLDC motor application
- Consumer electronics – computer hard drives, small cooling fans, cd/dvd players, etc. and also on modern appliances that operate quietly – such as washing machines, air conditioners, etc.
Electric Vehicles – Many electric vehicles including electric and hybrid cars, electric bicycles use BLDC motors. - The BLDC dynamo has a wide range of applications in many fields including robotics, industry, motion control systems, etc.